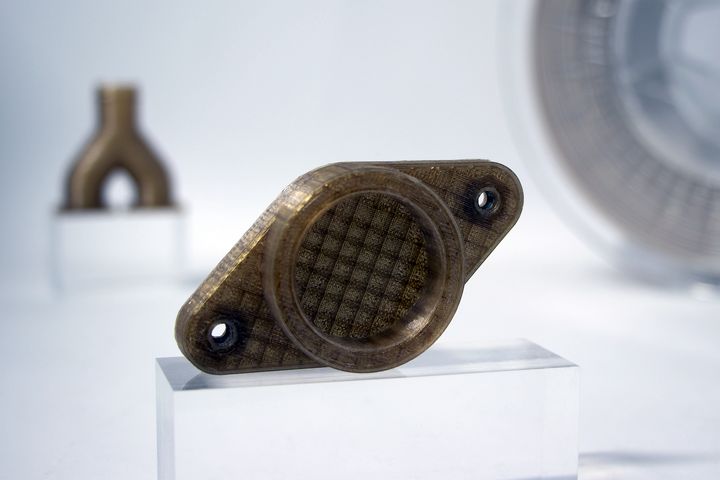
INTAMSYS has been focusing on the high-temperature 3D printing market for several years, releasing a series of machines capable of working with high-temp materials like PEEK, ULTEM and others at blisteringly high operating temperatures.
High-Temperature 3D Printing
These high-temp materials have been highly desirable of late as their thermal properties allow parts made from them to be used in a much wider set of applications, specifically where environmental temperatures are high. Unfortunately, very few 3D printers are properly optimized to print with them, as you need not only extremely high nozzle temperatures, but also enclosed chambers with significant internal heating.
INTAMSYS observed a problem with some PEEK materials during the course of their work: the PEEK materials typically used are not optimized for 3D printing applications; they were simply repurposed PEEK materials that were originally designed for other purposes, like injection molding or CNC milling.
Thus certain critical aspects of the 3D printing process were left with “default” properties. Specifically this involved the layer-to-layer adhesion that is typically the weakest part of a FFF part.
Victrex AM 200
INTAMSYS turned to UK-based Victrex, a large chemical company producing plastic materials and products. Victrex has been producing PAEK since 2018, but they have now released a 3D print-optimized variation they call “VICTREX AM 200”.
What’s different with this variation? It seems they have three main beneficial characteristics:
- Slower crystallization: this provides subsequent layers a bit more opportunity to bond with lower layers as they are deposited
- Lower melt temperature: This is obviously beneficial as less energy would be required to heat the material for 3D printing
- Fine-tuned viscosity: Extrusions become optimal as the viscosity matches the expected flow rates during 3D printing, as well as assisting in layer-to-layer bonding
Apparently VICTREX AM 200 also has a relatively low shrinkage factor, for which all 3D printer operators would be thankful.
Victrex explains:
“The PAEK-based new VICTREX AM filament has been designed and optimized specifically for AM. The excellent mechanical properties of PAEK are in demand for high performance parts. However, until now they were difficult to be fully realized in 3D printed parts with existing choices such as PEEK and PEKK. For example, repurposing injection molding PEEK into filament fusion AM, typically results in weak parts because of poor interlayer bonding. This new material is designed to address this weakness in printing PEEK. According to INTAMSYS´ experience using its manufacturing equipment, the VICTREX AM 200 filament has a higher Z-axis strength and has shown to date up to 80% strength in the XY direction with a better fused filament forming (FFF) printing adaptability than the existing PAEK materials.”
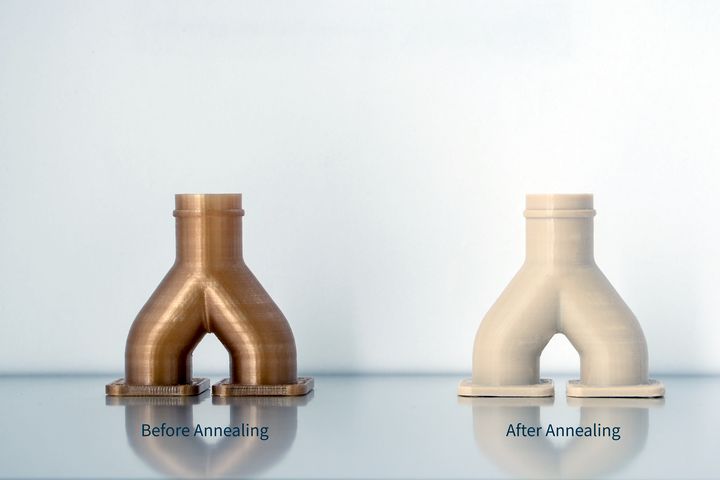
Charles Han, Founder and CEO at INTAMSYS, added:
“Our test results to date have shown that the VICTREX AM 200 filament has a better interlayer adhesion than other PAEK materials on INTAMSYS’ machines. Compared with unfilled PEEK, it is designed with slower crystallization, lower melt temperature, and a viscosity fine tuned to the filament fusion process, such as easier flow in the build chamber after leaving the nozzle. Higher flow in open air (low shear rates) also promotes interlayer bonding and stability during printing. All of this contributes to an improved interlaminar adhesion, easier printing (less shrink and warp), and a better suitability for FDM 3D printing, compared to other similar options, based upon the testing we have done at INTAMSYS up to this point.”
Stepping back, it’s interesting to see how the use of high-temperature materials is playing out. At first 3D printer operators were ecstatic at being able to produce parts with high-temperature materials. Now we’re taking a step beyond by using even better high-temp materials.